Business excellence
20 years of technology precipitation and professional coaching team to help companies achieve business excellenceERP scheme of automobile welding fixture industry
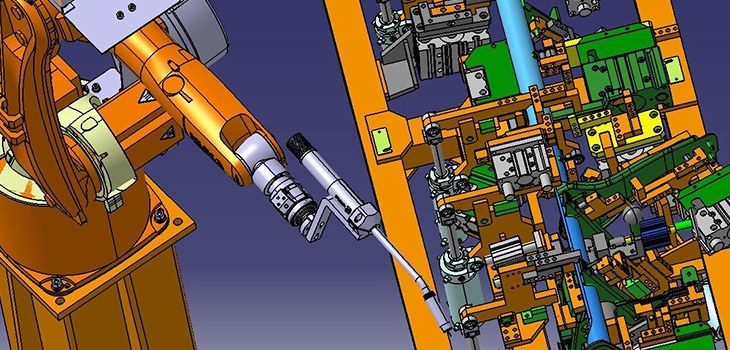
Characteristics and management problems of automobile welding fixture industry
With the development of China's automobile industry, welding technology has been used more and more in automobile production, and the requirements of production efficiency and product quality are higher and higher. Welding assembly fixture and various mechanized, semi-automatic and automatic welding assembly lines are also developed. Fangdee fixture ERP establishes and maintains fixture drawings, material list, design change data, workpiece process flow, work center and other basic data used in production. These data are the basis of project planning and scheduling, machine operation rate statistics, cost analysis and operation. The research shows that the cost of fixture design and manufacture accounts for 10% - 20% of the total cost.
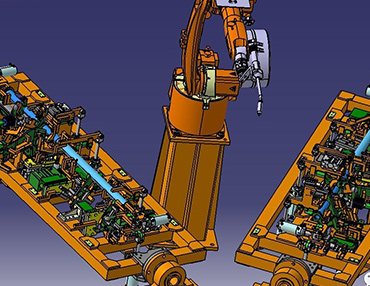
- According to the design fixture essentials, digital analog, product drawing, reference car process, welding process flow, preliminarily determine the number of fixtures.
- Design process layout according to process route and fixture quantity.
- Station beat, safety management and detailed process plan.
- It integrates with CAD, UG, CATIA and other design software, and automatically reads BOM list information to ensure consistency with design data.
- Fast realization of process design, drawing distribution, parts preparation, etc.
- Complete and hierarchical BOM provides correct basis for fixture production and purchase.
- Support batch and multiple release of BOM for purchase and production.
- It provides functions such as structure reference, BOM reuse and material reverse query, and supports direct import and export of Excel.
- View 2D or 3D models of fixture parts directly through BOM.
ERP solution for automobile welding fixture industry
Application of ERP management system of welding fixture in typical automobile body tooling manufacturing enterprises (body mold, body welding). This paper studies the product R & D characteristics of automobile tooling enterprises, combined with the new design mode of standardization, digitalization and intellectualization, and puts forward two main lines of "business management" and "project management", which makes the information management system of automobile tooling a big step forward on the network and digital platform.
- When determining the structure of each new set of jigs, according to the structural characteristics of each set of jigs, the system makes an effective project plan.
- Provide a variety of project planning template and plan node control scheme to quickly generate fixture project plan.
- You can set the schedule template of each node and quickly make the schedule automatically associated with each node.
- In the form of Gantt chart, manage the project schedule of each set of fixture, automatically follow up the implementation of the project through the project operation records of each department, and give early warning to the delayed plan.
- The project plan is automatically associated with the associated part processing plan, and the workshop part processing information is automatically fed back to the mold schedule to improve the project follow-up and effective control.
- Upload and download various forms and attachments related to the project for sharing and viewing.
- Directly view the production, purchase or inventory status of mold parts, blanks or standard parts from BOM, with highly shared information.
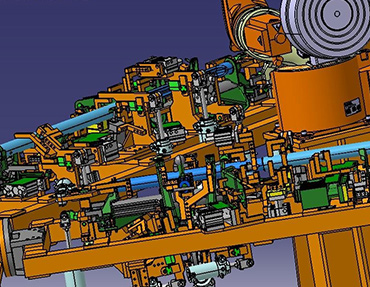